Introduction to Pressure Testing in Leak Detection
Pressure testing machines are widely used in industries to detect leaks in pipelines, vessels, and other pressure-containing systems. These machines operate by subjecting the system under test to a predetermined pressure, which allows the detection of leaks or weaknesses that could lead to system failures. The pressure testing process is essential to ensure the integrity of pipelines, tanks, and other equipment that operate under high pressure. A drop in pressure is a clear indication that a leak is present, which is why pressure testing is an essential preventive maintenance step.
The process of pressure testing works by applying a specified amount of pressure to a system. If the system is sealed correctly and has no structural faults, the pressure should remain constant. However, when a leak exists, the pressure will drop, and the extent of the pressure drop can be used to determine the severity and size of the leak. These changes in pressure, no matter how minor, can be detected by modern pressure testing machines, which are highly sensitive to fluctuations.
In the oil and gas industry, pressure testing machines are crucial for checking the integrity of pipelines that transport oil, natural gas, and other substances. Pipelines in these industries operate under extremely high pressures, and even a small leak can cause significant environmental damage and loss of product. Hydrostatic testing is commonly used in these settings because water is used as the pressure medium, and it’s safer compared to pneumatic testing. Hydrostatic tests are performed by filling the pipeline or vessel with water and increasing the pressure to the desired level. If the pressure holds steady, the system is deemed safe; if there’s a pressure drop, it indicates the presence of a leak.
Similarly, in the chemical industry, pressure testing is essential to ensuring that tanks and pipelines carrying hazardous chemicals do not leak. A leak in these systems could lead to dangerous spills, exposure to toxic substances, and catastrophic accidents. Therefore, pressure testing machines are employed to routinely test the pressure levels of containment systems and pipelines.
In water management systems, pressure testing machines help maintain the efficiency and safety of water pipes. A drop in pressure can indicate leaks in the system that could lead to water wastage or disruption of service to customers. Pressure testing in these systems is usually performed using hydrostatic tests, as water is both the medium being transported and the pressure testing fluid. Identifying leaks early ensures that the system can be repaired before it leads to system-wide failures or water contamination.
Construction projects also rely heavily on pressure testing. Before a new building is operational, plumbing, HVAC systems, and other high-pressure systems need to undergo pressure testing to confirm that they are free of leaks. For example, during the construction of a building, plumbing pipes are pressurized to ensure there are no weak spots or leaks. This prevents future water damage, inefficient systems, or health hazards due to water contamination.
Aerospace and automotive industries use pressure testing to check the integrity of fuel lines, hydraulic systems, and pressurized tanks. A failure in any of these components can lead to serious accidents or malfunctions, which is why pressure testing is critical to maintaining operational safety in these fields. Aircraft, for example, undergo pressure testing to ensure the integrity of their fuel systems and pressurized cabins.
The primary purpose of pressure testing is to identify weaknesses early on, preventing catastrophic failures and reducing repair costs. By identifying leaks during routine pressure testing, companies can address potential issues before they evolve into serious problems, which could lead to expensive repairs, loss of product, environmental damage, or system shutdowns.
Pressure testing also plays a key role in compliance. Many industries are required to follow safety regulations that mandate the regular testing of pipelines and vessels to ensure they meet industry standards. This is especially true in highly regulated sectors such as the oil, gas, and chemical industries, where regulatory authorities impose strict safety standards to prevent accidents and disasters.
Pressure testing is an indispensable part of leak detection in various industries. It helps ensure the safety and reliability of pipelines, vessels, and other systems by detecting leaks and weaknesses early. Pressure testing machines are crucial in providing a reliable, cost-effective method to monitor system integrity and prevent costly failures, environmental disasters, and regulatory violations.
The Science Behind Leak Detection Using Pressure Testing
The science behind leak detection using pressure testing machines relies on basic principles of fluid mechanics and the behavior of materials under pressure. Essentially, pressure testing is based on the idea that when a sealed system is subjected to pressure, the system should maintain that pressure if it is intact. If a leak is present, the pressure will drop, and this drop can be measured to determine the location and severity of the leak.
The most commonly used method in pressure testing is hydrostatic testing, where water is used as the pressure medium. Water, being incompressible, provides a safe testing environment. Hydrostatic testing is preferred over pneumatic testing (which uses air or gas) because air is compressible and can store significant amounts of energy, making pneumatic tests more dangerous in case of a failure. If a leak occurs during pneumatic testing, the release of compressed air can result in a sudden explosion. Water, on the other hand, poses much less of a safety risk due to its incompressibility.
When performing a hydrostatic test, the system is filled with water, and the pressure is gradually increased. The system is then monitored for any drop in pressure over time. If there is a leak, the pressure will begin to decrease. The amount of pressure lost over a specific time period indicates the size and nature of the leak. For example, a small leak will cause a gradual decrease in pressure, while a large leak will lead to a rapid drop in pressure.
Pressure sensors in the testing machine are highly sensitive and capable of detecting even minute fluctuations in pressure. These sensors provide real-time data that can be analyzed to assess the condition of the system. Many modern pressure testing machines use digital sensors, which offer higher accuracy and the ability to monitor pressure over extended periods. Digital sensors can also log data for future analysis, which is crucial for identifying patterns or recurring problems in systems that may need frequent repairs.
In pneumatic testing, air or gas is used instead of water. Although this method is faster and more suitable for certain applications, it comes with greater risks. When using pneumatic testing, the system is pressurized with gas, and any drop in pressure indicates a leak. Pneumatic testing is often used for systems that cannot be easily filled with water, such as those in colder environments where water may freeze. However, due to the compressibility of gas, there is always a risk of dangerous over-pressurization, which is why it is typically used for smaller-scale systems or in controlled environments.
Another important consideration in pressure testing is temperature fluctuations. Temperature can have a significant impact on the behavior of the testing fluid and the system under test. For example, changes in temperature can affect the volume of gas or water, potentially causing minor variations in pressure that are unrelated to a leak. To address this, advanced pressure testing machines are equipped with temperature compensation mechanisms. These mechanisms adjust the pressure readings to account for temperature changes, ensuring that the results are accurate regardless of external environmental factors.
The process of leak detection using pressure testing is highly dependent on accurate data analysis. Modern pressure testing machines can log pressure readings over time, creating a detailed profile of how the pressure behaves throughout the test. This data is then analyzed to detect trends or inconsistencies. For example, a slight and consistent drop in pressure over several hours could indicate a small leak, whereas an abrupt and rapid drop would suggest a larger, more critical leak.
Many pressure testing machines come with advanced algorithms that can predict the likelihood of a leak before it occurs, based on historical data and sensor readings. These predictive models allow for proactive maintenance, where potential leaks are identified before they become a serious problem.
In some cases, if a leak is detected, additional leak detection methods such as ultrasonic testing, tracer gases, or dye injection can be used to precisely locate the source of the leak. These techniques work in conjunction with pressure testing to help pinpoint the exact location of a leak, especially in complex systems with long pipelines or intricate networks.
The science behind leak detection using pressure testing involves understanding the behavior of pressure within a system and using sensitive equipment to detect any deviations from expected readings. Whether through hydrostatic or pneumatic testing, the underlying principle remains the same: pressure loss indicates a problem. Modern pressure testing machines enhance the accuracy and safety of this process through the use of digital sensors, temperature compensation, and predictive algorithms, making them an invaluable tool in the detection and prevention of leaks across a wide range of industries.
Types of Pressure Testing Machines and Their Applications
Pressure testing machines are critical tools used to assess the integrity of various systems, including pipelines, vessels, and tanks. These machines come in different types, each suited for specific testing applications, and understanding their functionalities helps ensure that the right machine is selected for the task at hand. The primary types of pressure testing machines include digital pressure testing machines, analog pressure testing machines, and automated pressure testing systems, with each offering unique features suited for particular industrial needs.
Digital Pressure Testing Machines: These machines are the most common in modern leak detection practices. Digital pressure testers use advanced digital sensors to provide highly accurate pressure readings in real-time. These machines are equipped with features that allow them to monitor and log pressure changes over a specified period, making them invaluable for both short-term tests and long-term monitoring of system integrity. Digital pressure testing machines often come with built-in data logging capabilities, which store pressure readings for analysis, trend identification, and later reference. The data collected can be exported to external devices or cloud platforms for detailed analysis.
Digital machines are especially advantageous in oil and gas and chemical industries, where the integrity of pipelines, storage tanks, and pressurized systems must be verified frequently to ensure safety and avoid leaks that could lead to catastrophic incidents. Digital pressure testing systems also feature temperature compensation algorithms that adjust for fluctuations in ambient conditions, ensuring that pressure readings remain accurate even under varying environmental factors. Additionally, many digital models come with remote monitoring capabilities, which allow operators to oversee the testing process without being physically present on-site. This capability is particularly useful for high-risk environments such as offshore oil rigs or remote pipeline installations.
Analog Pressure Testing Machines: While digital pressure testing machines have become the standard, analog machines still have their place in certain applications. Analog testers use mechanical or dial gauges to monitor pressure, providing a visual reading of pressure values. These machines lack the sophisticated data logging and remote monitoring features of their digital counterparts but are still suitable for simple pressure tests. Analog testing machines are often found in older installations or less complex systems that do not require real-time data analysis.
In some cases, analog pressure testing machines are preferred because of their cost-effectiveness and reliability in environments where high-tech features are unnecessary. In water distribution systems, for example, analog machines may be used for quick spot checks to ensure that the pressure in pipelines is within acceptable limits. Analog pressure testing systems are also used in small-scale industries or for temporary setups where digital systems are either too expensive or unnecessary.
Automated Pressure Testing Systems: The third category of pressure testing machines is automated systems, which are typically used for large-scale or complex operations. These systems are designed to streamline the process of pressure testing by automating various functions, such as pressure application, monitoring, and data logging. Automated machines are often integrated into industrial control systems, allowing operators to remotely initiate, monitor, and analyze tests without direct involvement in the physical testing process.
Automated systems are particularly beneficial in large-scale industrial settings, such as refineries, power plants, and petrochemical facilities, where multiple tests need to be conducted simultaneously or in environments where human presence is limited due to safety reasons. These systems can perform a series of tests, record detailed pressure data, and even analyze results automatically. Some automated pressure testing machines are capable of performing tests on multiple systems at once, increasing efficiency and reducing the time needed for comprehensive testing. This type of system is especially important in the oil and gas industry, where thousands of kilometers of pipeline may require frequent pressure tests. Automated machines can efficiently conduct these tests, ensuring that no segment of the system goes unchecked.
Each of these pressure testing machines has distinct advantages, depending on the application. Digital pressure testing machines offer accuracy, real-time monitoring, and the ability to handle complex data, making them ideal for large-scale industries where the risk of leaks can have devastating consequences. Analog machines, while simpler, still provide essential pressure testing capabilities at a lower cost. Automated systems, on the other hand, provide the highest level of efficiency and are ideal for industries requiring continuous testing on a large scale. By selecting the appropriate pressure testing machine based on the specific needs of the operation, companies can ensure that their pressure systems are safe, reliable, and fully functional.
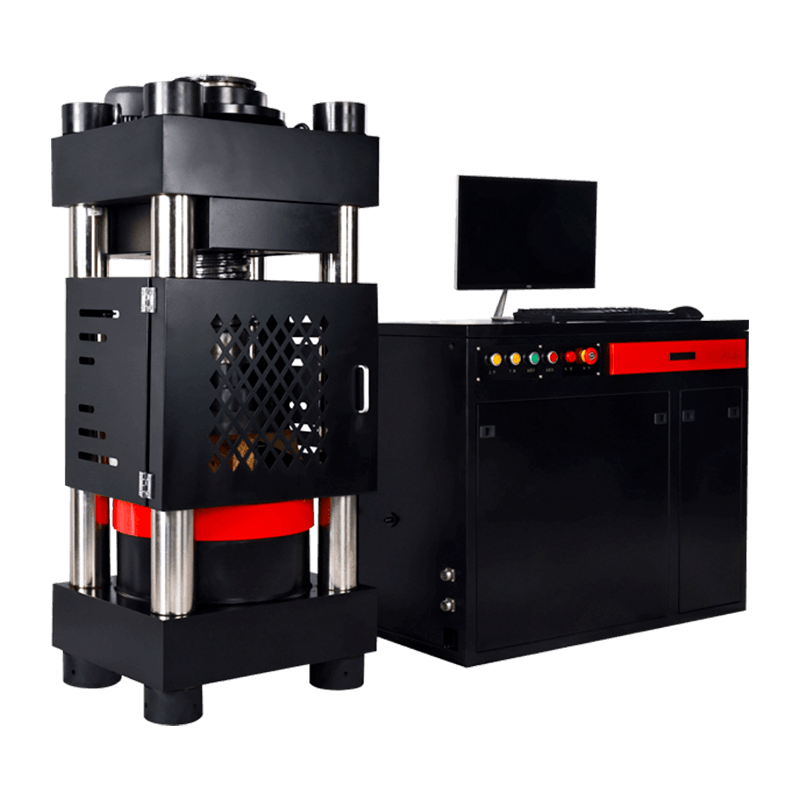
Project/Indicator/Model
|
AW-3000
|
YAW-5000
|
The maximum test force of the testing machine
|
3000KN
|
5000KN
|
Accuracy rating
|
1
|
Level 1
|
Relative error of the test force indication
|
±1% or Less
|
±1% or Less
|
Compress the maximum clear space
|
360mm
|
360mm
|
Maximum piston stroke
|
70mm
|
200mm
|
Effective test width
|
330mm
|
550mm
|
Power supply
|
AC380V±10%, 2.0kW
|
AC380V±10%, 2.0kW
|
Dimensions of the main unit (L×W×H)
|
540×675×1300mm
|
900×600×1660mm
|
Control cabinet dimensions (L×W×H)
|
1000×550×800mm
|
1000×550×800mm
|
Net weight Kg
|
2000KG
|
3300kg
|
|
The Role of Pressure Testing in Preventing System Failures
Pressure testing plays a vital role in preventing system failures across various industries. Its primary purpose is to ensure the structural integrity of systems that operate under pressure, such as pipelines, tanks, and vessels. Systems exposed to high-pressure environments are more prone to wear and tear over time, making regular testing essential for identifying potential weaknesses. Pressure testing provides early detection of issues, allowing for corrective actions before failure occurs, which helps prevent costly repairs, environmental hazards, and safety risks.
Early Detection of Leaks: One of the primary benefits of pressure testing is its ability to detect leaks early. Leaks in pressurized systems, whether small or large, can have severe consequences if left undetected. For example, in the oil and gas industry, a small pipeline leak could result in a catastrophic spill, leading to significant environmental damage, regulatory fines, and reputational harm. By conducting regular pressure tests, companies can identify even the smallest leaks, ensuring that systems are repaired before a leak can cause significant problems. This proactive approach to leak detection reduces the risk of leaks going unnoticed for long periods, which can result in substantial economic and environmental costs.
Preventing Equipment Failure: Pressure testing helps prevent equipment failure by identifying weak points in the system. For instance, pipelines that have been exposed to external forces or internal corrosion are more susceptible to failure. Pressure tests can detect areas where the material has become weak or compromised. In chemical plants or refineries, where hazardous substances are transported under high pressure, a failure could result in dangerous spills, explosions, or fires. Pressure testing machines can be used to simulate the conditions that the system will face in real-world operation and ensure that it can withstand those conditions without failing. This preventative maintenance minimizes the chances of unplanned downtime, ensuring that operations continue without interruption.
Compliance with Regulatory Standards: Many industries, especially those dealing with hazardous materials, are subject to strict safety and environmental regulations. Regular pressure testing ensures compliance with these standards by verifying that systems meet the required safety specifications. For example, in the nuclear energy sector, pressure testing is crucial to ensuring the integrity of reactor coolant systems and safety valves. Failure to comply with regulatory standards can lead to costly fines, shutdowns, and even the suspension of operations. By conducting regular pressure tests and documenting the results, companies demonstrate their commitment to maintaining safety and complying with industry regulations.
Reducing Maintenance Costs: Regular pressure testing can help companies identify potential problems before they lead to system failure. This early detection prevents the need for extensive repairs, which can be both costly and time-consuming. For example, in water distribution systems, detecting leaks early allows for the repair of small sections of pipes instead of replacing entire segments. Regular testing also helps extend the lifespan of equipment by identifying areas that require maintenance or replacement before they fail completely. This predictive maintenance approach ensures that resources are used efficiently and that maintenance costs are kept under control.
Improving System Reliability and Efficiency: Regular pressure testing ensures that systems operate at their optimal efficiency. For example, in pneumatic systems, leaks or reduced pressure can decrease the overall efficiency of the system, leading to higher energy consumption and wasted resources. Pressure tests help identify and rectify issues that could lead to inefficient system performance, improving both energy efficiency and overall reliability. This is particularly important in industries where downtime or inefficiency can result in significant financial losses, such as in manufacturing or chemical processing.
Safety Assurance: Pressure testing is also crucial for ensuring the safety of personnel working around high-pressure systems. A failure in a pressurized system can lead to serious accidents, including explosions, toxic gas leaks, or equipment malfunctions that could endanger workers. Pressure testing helps to ensure that systems are properly sealed and can withstand the stresses they will face during operation. In industries like aerospace, nuclear energy, and oil and gas, safety is paramount, and pressure testing is a critical component of maintaining a safe working environment. Regular testing allows operators to address issues before they pose a danger to personnel, creating a safer workplace overall.
How to Perform a Pressure Test to Detect Leaks
Performing a pressure test to detect leaks is a critical process for ensuring the integrity of pressurized systems. Whether you are testing a pipeline, storage tank, or vessel, the procedure involves several stages that must be carefully followed to guarantee reliable results. Pressure testing is used in industries ranging from oil and gas to chemical manufacturing, water distribution, and construction. A proper understanding of the steps involved ensures that the system is thoroughly tested for leaks and weaknesses before it is put into operation.
Preparing the System for Testing:
Before beginning a pressure test, the system must be properly prepared. This preparation phase is crucial to ensure accurate results and the safety of the personnel conducting the test. Start by thoroughly cleaning the system to remove any debris, dirt, or scale buildup that could affect the accuracy of the test. This is particularly important in hydraulic systems or water pipelines, where dirt or blockages can interfere with the pressure readings.
Next, inspect the system for any visible signs of damage, wear, or corrosion. Check seals, valves, and joints for signs of degradation that could compromise the test. If any obvious issues are detected, they should be addressed before proceeding with the test. The pressure test is meant to simulate normal operating conditions, so ensuring the system is fully functional is key to avoiding false results.
Once the system is cleaned and inspected, it should be sealed. For pipelines, this involves ensuring that all valves are tightly closed, and for tanks or vessels, that all access points are properly sealed. This ensures that the system can maintain pressure without leakage at any connection points during the test.
Selecting the Right Pressure Medium:
The choice of pressure medium is an important factor in performing the test. The two primary options for pressure testing are hydrostatic testing and pneumatic testing.
Hydrostatic Testing: This method uses water as the testing medium. Water is ideal because it is incompressible, which means that any drop in pressure is a clear indication of a leak. Water is also safe to use since it doesn’t store energy the way gases do. For hydrostatic testing, the system is filled with water, and pressure is applied gradually. The pressure level will depend on the type of material being tested and its specifications. For example, a pipeline made of steel may undergo testing at a pressure level higher than that of a plastic pipe.
Pneumatic Testing: Pneumatic testing uses air or another gas to pressurize the system. While pneumatic tests are quicker and more suitable for certain types of systems, they are also riskier due to the compressibility of gases. A leak in a system under pneumatic pressure can result in a violent release of energy, making this method more hazardous and typically reserved for smaller systems or non-hazardous environments. Pneumatic tests should be performed with great care, ensuring that all safety protocols are followed.
Applying Pressure to the System:
Once the system is prepared and the pressure medium is selected, the next step is to apply pressure to the system. The pressure is gradually increased to the desired test level, which is typically higher than the normal operating pressure to ensure that the system can withstand greater stress. The test pressure will vary depending on the system’s design specifications. For example, a natural gas pipeline may be tested at a pressure several times higher than its operating pressure to ensure its durability under extreme conditions.
During this phase, a pressure testing machine or a digital pressure gauge is used to monitor the pressure levels. These machines provide real-time data and allow the operator to observe fluctuations in pressure. Modern pressure testing systems often feature automatic controls that ensure the pressure is increased gradually and steadily, reducing the risk of overpressurizing the system.
Monitoring and Analyzing Pressure Readings:
Once the system has been pressurized, it is important to monitor the pressure readings carefully. A stable system should maintain the desired pressure level without significant fluctuation. The pressure is monitored over a specified period (usually several minutes to hours, depending on the test type) to ensure that it remains constant. If a leak is present, the pressure will begin to drop. The rate at which the pressure drops can help determine the severity of the leak. A small leak will cause a slow, gradual decrease in pressure, while a large leak will result in a rapid pressure drop.
The readings should be recorded at regular intervals, and any changes in pressure should be logged. This data provides a record of the test, which is useful for post-test analysis and determining the location and extent of any leaks. Some advanced pressure testing systems offer real-time data logging that can be accessed remotely, providing additional convenience and safety for technicians.
Identifying and Locating Leaks:
Once the pressure has been maintained for the required duration, it is time to analyze the results. If the pressure has remained constant throughout the test, the system is considered to be leak-free. However, if there has been a drop in pressure, further investigation is needed to locate the leak. Various methods can be used for this purpose:
Visual Inspection: In some cases, a visual inspection of the system may reveal the source of the leak. For example, a water pipeline might show visible signs of water seepage at a joint or weld. However, this method is not always sufficient, especially for hidden leaks.
Ultrasonic Testing: For systems where leaks are not visible, ultrasonic testing can be used to pinpoint the leak’s location. This method uses sound waves to detect leaks, as escaping fluids or gases often emit specific acoustic signals that can be detected with sensitive equipment.
Dye Testing: In some cases, a dye or tracer gas can be introduced into the system to make leaks more detectable. This method is particularly useful in smaller systems or areas that are hard to access.
Once the leak is located, it can be repaired, and the system can undergo another pressure test to ensure the repair was successful.
Completing the Pressure Test:
After identifying and repairing any leaks, the system should be retested to confirm that the repairs were effective. If the system passes the pressure test without any further drop in pressure, it can be considered leak-free and safe for operation. The test results should be recorded, including any leaks identified, repairs made, and the final pressure readings.
Challenges in Leak Detection and How Pressure Testing Machines Overcome Them
Leak detection, especially in large or complex systems, is a challenging process that requires precise equipment and detailed analysis. Despite the effectiveness of pressure testing machines, several factors can complicate leak detection, making it difficult to identify small or hidden leaks. Some of the main challenges faced during leak detection and how pressure testing machines address these issues are discussed below.
Small or Slow Leaks:
One of the most significant challenges in leak detection is identifying small or slow leaks, especially in large systems like pipelines or storage tanks. Small leaks may not result in an immediate drop in pressure, making them hard to detect with conventional methods. Over time, however, these leaks can cause significant damage, leading to loss of product, wasted energy, or environmental hazards.
Modern digital pressure testing machines address this issue by providing highly sensitive pressure measurements. These machines can detect even the smallest fluctuations in pressure, allowing for the identification of slow leaks that may otherwise go unnoticed. Additionally, many digital pressure testers are equipped with data logging features that track pressure changes over time. This allows technicians to observe trends and identify gradual pressure loss that may indicate a developing leak.
External Environmental Factors:
Temperature fluctuations, humidity, and external pressure changes can affect the accuracy of pressure readings. For instance, as the temperature rises or falls, the volume of gases or liquids used in the testing process can change, leading to inaccurate readings. This can make it difficult to differentiate between a pressure drop caused by a leak and one caused by environmental factors.
Many modern pressure testing machines are equipped with temperature compensation systems. These systems adjust the readings to account for temperature changes, ensuring that the results are accurate regardless of external environmental conditions. This feature is particularly useful in industries like oil and gas and chemical processing, where systems are often subjected to extreme temperatures or harsh conditions.
Complex Systems and Hard-to-Reach Areas:
In large and intricate systems, such as offshore oil rigs or extensive pipeline networks, it can be difficult to access all parts of the system for testing. Some areas may be physically inaccessible or difficult to inspect due to their size or location. In these cases, pressure testing machines can be equipped with remote monitoring capabilities, which allow operators to conduct tests and monitor pressure levels without being physically present on-site.
Advanced pressure testing machines can also be integrated with robotic or drone technology to inspect hard-to-reach areas. This is particularly useful for systems that are located in hazardous environments or areas where human presence is limited, such as underwater pipelines or remote industrial facilities.
System Size and Testing Duration:
For large systems, pressure testing can be a time-consuming process. Conducting pressure tests on thousands of kilometers of pipeline or large storage tanks may require significant time and resources. Furthermore, the larger the system, the more complex the test becomes. Monitoring pressure levels across a vast network can be challenging, and even minor leaks can be difficult to identify.
To overcome these challenges, automated pressure testing systems have been developed to handle large-scale testing more efficiently. These systems allow for simultaneous testing of multiple sections of the system, significantly reducing the time required to complete a full test. Automated systems can also be programmed to conduct routine tests at regular intervals, ensuring that potential issues are detected early before they escalate.
Detection of Multiple Leaks:
In some cases, a system may have multiple leaks, which can complicate the testing process. For example, a large pipeline may have several small leaks scattered throughout the network. Identifying all these leaks can be time-consuming and difficult, especially if they are not immediately apparent during the pressure test.
Advanced pressure testing machines equipped with sophisticated algorithms can analyze the data from pressure sensors and identify multiple leaks simultaneously. These machines can calculate the flow rate of pressure loss and pinpoint the areas of greatest concern, reducing the time and effort required to detect and repair multiple leaks.
The Importance of Pressure Testing Machines in Ensuring Safety and Compliance
Pressure testing machines are a critical tool in ensuring the safety, reliability, and compliance of systems that operate under pressure. Whether in pipelines, storage tanks, pressure vessels, or any other pressurized systems, maintaining integrity is paramount to prevent hazardous failures. Pressure testing not only protects personnel, assets, and the environment but also ensures that the system adheres to industry standards and regulatory requirements. The importance of pressure testing machines extends beyond just leak detection; they play a vital role in maintaining the overall safety of industrial operations, protecting both human health and the environment.
Preventing Catastrophic Failures:
The primary function of pressure testing machines is to prevent catastrophic failures by identifying weaknesses or flaws in pressurized systems before they cause damage. For example, in oil and gas pipelines, a small crack or defect can lead to significant leaks, which could result in explosions, fires, or environmental disasters such as oil spills. A pressure test simulates operating conditions and exposes the system to higher pressures than it would typically encounter in operation, identifying potential failure points. The test enables technicians to identify weak spots and reinforce them, ensuring the pipeline can withstand the pressures it will face during normal operation without failure.
In the chemical industry, pressure vessels and tanks store hazardous substances, and any rupture or leak can result in catastrophic consequences, including chemical spills, fires, or toxic exposure to workers and the environment. By testing these systems under pressure before they are put into operation, manufacturers ensure that any potential safety issues are detected and addressed in advance, reducing the risk of hazardous incidents.
Compliance with Industry Standards and Regulations:
In highly regulated industries such as oil and gas, nuclear power, chemical manufacturing, and pharmaceuticals, there are strict regulations governing the safety and operational integrity of pressure systems. These regulations require that pressure vessels, pipelines, and storage tanks undergo routine pressure testing to ensure their structural integrity. For instance, the American Society of Mechanical Engineers (ASME) and the American Petroleum Institute (API) set guidelines for pressure testing systems used in the oil and gas industry, and failure to comply with these standards can result in costly fines, shutdowns, or loss of certification.
Pressure testing machines play an essential role in demonstrating compliance with these safety and quality standards. When a system passes a pressure test, it can be certified as being safe for operation. For example, pressure testing is required before pipelines are put into service to ensure they meet the structural and safety standards set forth by regulatory bodies. This helps mitigate the risk of non-compliance, which could lead to reputational damage, legal consequences, and fines.
Enhancing Worker Safety:
The safety of workers is a top priority when dealing with systems under high pressure. Pressure testing machines help mitigate risks that could threaten personnel in hazardous environments. For example, in offshore oil platforms, workers are exposed to high-risk situations when handling equipment that operates under extreme pressures. Pressure testing ensures that pipes, valves, and other critical components are capable of withstanding the operating pressures, reducing the likelihood of failures that could cause dangerous accidents. By identifying weak points and addressing them before full operation, pressure testing machines reduce the risk of incidents that could cause injuries or fatalities.
In industries like aerospace, where pressurized systems are part of aircraft design, testing ensures that every component, including fuel lines, hydraulic systems, and pressure cabins, is able to perform under the extreme conditions it will face during flight. The rigorous pressure testing ensures that these systems will function as intended, without risk of sudden failure or malfunctions that could jeopardize the safety of the crew and passengers.
Environmental Protection and Mitigation of Hazardous Spills:
Pressure testing machines are also instrumental in environmental protection. Leaks in pressurized systems can result in the release of harmful substances, such as oil, chemicals, or gases, into the environment. A small leak in a pipeline carrying hazardous materials can have disastrous environmental consequences. Pressure testing machines ensure that these pipelines, tanks, and vessels are leak-proof, preventing the accidental release of dangerous substances into the air, water, or soil.
For example, in water treatment facilities, pressure testing is used to check for leaks in pipelines that transport drinking water. A leak in such systems could not only waste valuable water resources but also introduce contaminants, compromising the health of the population. By testing these systems regularly, utilities can identify leaks early and avoid costly repairs or public health issues.
Improving Operational Efficiency and Reliability:
Beyond safety, pressure testing machines also help improve the overall efficiency and reliability of pressurized systems. A well-maintained system that has undergone regular pressure testing will operate more efficiently and last longer. For example, in HVAC systems in commercial buildings, regular pressure testing ensures that the system is properly sealed and functioning. If a leak is detected and repaired early, the system will be able to operate more efficiently, reducing energy consumption and lowering operational costs.
Similarly, in industrial facilities where pressurized systems are used to transport materials, pressure testing helps ensure that the system can handle the demands placed upon it. By regularly testing the system, manufacturers can optimize system performance, prevent unplanned downtime, and ensure that production targets are met without delays caused by system failures.
Ensuring Long-Term Maintenance and Cost Savings:
Pressure testing is also an essential part of preventive maintenance. By conducting pressure tests at regular intervals, companies can identify potential weaknesses and repair them before they lead to more costly and extensive damage. For example, in petrochemical plants, pressure testing is used to assess the integrity of pipelines that transport raw materials or finished products. Early detection of leaks or structural weaknesses allows for targeted repairs, which can extend the lifespan of the pipeline and prevent costly emergency repairs that could disrupt operations.