New Challenges Facing Construction Project Quality
With the acceleration of urbanization and the continuous advancement of construction technology, the construction industry has ushered in unprecedented development opportunities worldwide. However, behind these rapid developments, construction project quality management is facing increasingly severe challenges. In particular, in the quality management of basic materials such as steel bars, there are still many problems that need to be solved. These problems not only directly affect the quality and safety of construction projects, but also the safety of people's lives and property and the sustainable development of society.
Among these basic materials, steel bars are one of the most critical components of building structures. The quality of steel bars directly determines important indicators such as the bearing capacity, seismic performance, and durability of buildings. Once a building suffers structural failure due to steel bar quality problems, it will not only cause huge economic losses, but also pose a serious threat to public safety. Therefore, how to ensure the quality of basic building materials such as steel bars, especially their bending performance, has become a core issue in the current construction project quality management.
Challenges of steel bar quality management
The quality management problems of steel bars are mainly reflected in the following aspects:
Unqualified products in the production and supply of steel bars: Although the production process of steel bars has made great progress in recent years, there is still a phenomenon of unqualified steel bars flowing into construction sites in the market. Some unqualified steel bars fail to meet the design and construction requirements due to substandard raw materials, insufficient heat treatment, lax control of the rolling process, etc. in the production process, and are prone to problems such as insufficient strength and poor corrosion resistance.
Improper transportation and storage of steel bars: In construction projects, the transportation and storage of steel bars are also important factors affecting their quality. During transportation, steel bars are easily affected by mechanical damage, environmental humidity and other factors, causing surface corrosion or bending deformation. During storage, if the steel bars are not properly protected, the steel bars exposed to the air will rust due to long-term contact with the humid environment, thereby reducing their bearing capacity and durability.
Irregular steel bar connection and construction: Even if the steel bar itself is of qualified quality, in the actual construction process, if the steel bar is improperly connected, tied loosely or welded loosely, it will affect the bearing capacity of the steel bar and the bond between the steel bar and the concrete. Especially in some important structural parts, the bending performance of the steel bar and its connection method may become the key factors in determining the safety of the building.
Inconsistent and poor implementation of quality inspection standards: In the quality inspection process of steel bars, many engineering units rely on traditional manual inspection methods, which have problems such as inconsistent judgment standards, non-standard operations and distorted inspection data. Moreover, in some projects, due to cost considerations and progress pressure, some construction parties may ignore the quality inspection of steel bars or lower the inspection standards, resulting in unqualified steel bars entering the construction site.
The key role of steel bar bending performance in building safety and durability
The bending performance of steel bars is one of the important indicators to measure their quality. As the "skeleton" of the building, steel bars bear huge structural pressure and play a load-bearing role together with concrete. The main function of steel bars in building structures is to provide tension and reinforcement. When buildings encounter external forces such as earthquakes and wind pressure, steel bars can effectively absorb and disperse these forces to ensure the stability of the structure.
However, the bending performance of steel bars is directly related to their deformation capacity and crack resistance when subjected to external forces. If the bending performance of steel bars does not meet the standards, it may lead to the following serious problems:
Insufficient strength, easy to break or deform: The strength and elastic modulus of steel bars determine their deformation capacity when subjected to external forces. If the bending performance of steel bars is poor, it may cause breakage or excessive deformation during construction or use, thereby affecting the bearing capacity of the overall structure. Especially in seismic design, the excellent bending performance of steel bars is the basis for buildings to effectively absorb earthquake energy and avoid structural instability.
Affect the bonding performance of concrete and steel bars: The bending performance of steel bars is closely related to the bonding performance of concrete. After the steel bars are bent, if cracks or damage appear on their surface, the bonding force between the steel bars and concrete may be reduced, thereby affecting the force performance of the entire structure, resulting in a decrease in the compressive capacity of the building and increasing the risk of structural damage.
Reduce the durability of the building structure: The unqualified bending performance of the steel bar often means that the steel bar has poor corrosion resistance in harsh environments. When the building encounters moisture, acid and alkali corrosion and other factors, the corrosion rate of unqualified steel bars will accelerate, which will in turn affect the durability and service life of the building.
Increase construction costs and construction period: Poor bending performance of steel bars may lead to frequent steel bar damage and failure to meet design requirements during construction, which not only increases the complexity of construction, but may also lead to project delays and ultimately increase costs.
Basic concept of rebar bending testing machine
Rebar bending testing machine is a high-precision equipment specially used to test the bending performance of rebar, which is widely used in the construction industry and material testing industry. It can simulate various bending conditions that rebar may encounter during construction and use, and ensure that the rebar meets the requirements of building design and relevant standards. By performing precise cold bending and reverse bending tests on rebar, rebar bending testing machine provides a scientific basis for the quality control of rebar and plays an important role in ensuring the safety and durability of buildings.
The application of rebar bending testing machine is not limited to the quality inspection of rebar, but also plays a vital role in the construction quality and long-term structural safety in construction projects. With the continuous improvement of building material standards and engineering quality management requirements, the technical development of rebar bending testing machine is also constantly improving, thereby improving its detection accuracy, efficiency and automation.
Definition of rebar bending testing machine
Rebar bending testing machine is a professional equipment used to test the bending performance of rebar. Its main function is to perform various tests such as bending, reverse bending, cold bending, etc. on rebar by simulating the bending operation in actual construction to determine the mechanical properties and bending capacity of rebar under different conditions. These tests can verify whether the steel bar meets the relevant quality standards and engineering design requirements, especially the strength, ductility, fatigue resistance and crack resistance of the steel bar.
The steel bar bending testing machine bends the steel bar by applying a certain force or load, and then measures the bending degree of the steel bar as well as the stress and deformation generated during the bending process. These data can provide a comprehensive analysis of the quality of the steel bar and help relevant personnel make a judgment on whether the quality is qualified or not.
Main functions of the steel bar bending testing machine
The main functions of the steel bar bending testing machine include the following aspects:
Steel bar bending performance test: This is one of the core functions of the steel bar bending testing machine. The steel bar bending testing machine can test the bending deformation ability of the steel bar under a certain external force, and determine whether it can withstand the predetermined stress without breaking or excessive plastic deformation in actual use.
Cold bending test: The steel bar cold bending test is one of the common applications of the steel bar bending testing machine. The cold bending test bends the steel bar at room temperature by applying a certain bending force to test whether it can complete the specified bending angle without breaking. Cold bending test is mainly used to evaluate the plastic deformation capacity of steel bars to ensure that the steel bars will not brittle fracture when bent during construction.
Reverse bending test: Reverse bending test is an important function of the steel bar bending testing machine. Reverse bending refers to the reverse bending test of the steel bar after a bending, which simulates the reverse bending stress that the steel bar may encounter during construction. Through the reverse bending test, it can be verified whether the steel bar has cracks, fractures or mechanical properties have decreased during multiple bending processes. This function is particularly suitable for quality inspection of construction projects where steel bars are repeatedly stressed.
Detect the elastic modulus and yield strength of steel bars: Elastic modulus and yield strength are important mechanical performance indicators of steel bars. The steel bar bending testing machine can calculate the elastic modulus and yield strength of steel bars through the mechanical data measured during the bending process, providing a scientific basis for the use of steel bars and ensuring that they meet the design specifications and construction requirements.
Test the fracture elongation of steel bars: In addition to bending strength, the ductility of steel bars is also one of the important criteria for evaluating their quality. Through the bending test, the steel bar bending testing machine can test whether the steel bar can undergo a certain degree of plastic deformation during the bending process without brittle fracture, which is crucial to ensure the seismic performance and safety of the building structure.
Data recording and analysis function: Modern steel bar bending testing machines are usually equipped with advanced data acquisition and analysis systems, which can record the mechanical data during the bending process in real time and analyze and process them. These data can not only be used to evaluate the performance of the steel bar, but also generate test reports to provide detailed test results for quality management personnel.
Application of steel bar bending testing machine in cold bending and reverse bending tests
Application of cold bending test
Cold bending test is usually used to check the bending performance of steel bars under normal temperature conditions, especially in the steel bar processing process, cold bending is one of the common operations. Through the cold bending test, the steel bar bending testing machine can verify whether the steel bar has sufficient ductility to ensure that it will not break when bent at the construction site. Cold bending test is a common quality control method in the steel bar production process, especially for seismic structures, prestressed structures and other projects with high requirements for steel bar performance.
The process of cold bending test includes fixing the steel bar on the testing machine, and then applying force according to the predetermined bending angle to test whether the steel bar can be bent smoothly without breaking. If the steel bar breaks or cracks during the cold bending process, it means that there is a problem with the quality of the steel bar and it may not be suitable for use in the project.
Application of reverse bending test
The reverse bending test is mainly used to test the resistance of steel bars when they are subjected to multiple bending or reverse bending. Steel bars in construction projects are often subjected to repeated loads, especially in seismic design, the reverse bending performance of steel bars is crucial. The steel bar bending testing machine can simulate the reverse bending conditions that steel bars may encounter in building structures and check their performance during reverse bending.
Through the reverse bending test, the fatigue strength and mechanical properties of steel bars after repeated bending can be evaluated to ensure that they will not degrade due to repeated loads during long-term use, and ensure that the building structure always maintains good safety during long-term use.
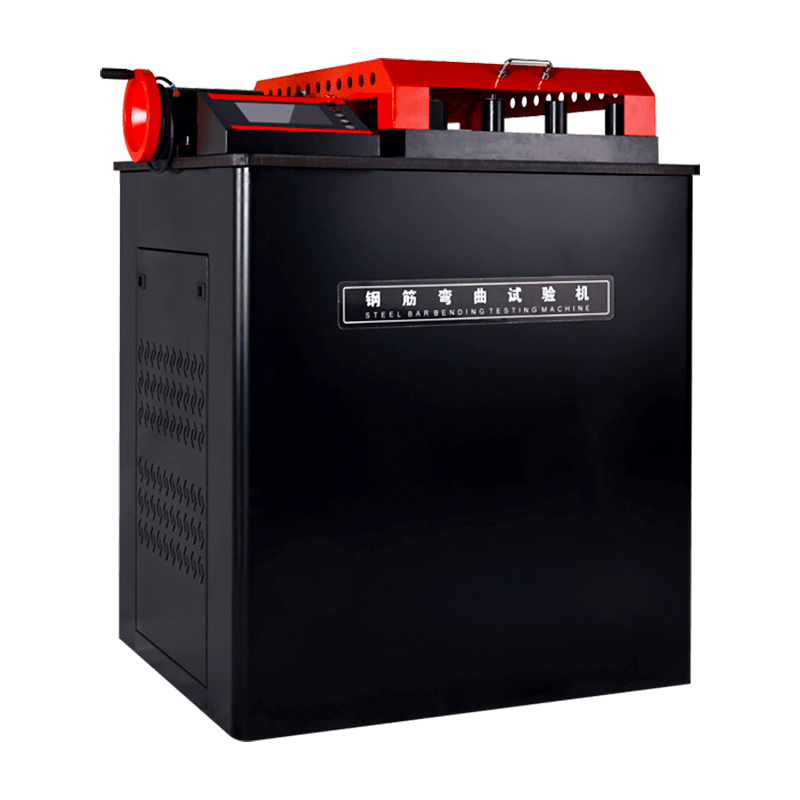
Project/Indicator/Model
|
GW-40A
|
Bend diameter range
|
φ6-φ40mm
|
The forward bending angle of the rebar
|
0°-180° can be set arbitrarily
|
The rebar is bent in the opposite direction
|
0°-180° can be set arbitrarily
|
Working disc speed
|
≤1.4r/min
|
Diameter of the working plate
|
φ570mm
|
Power supply
|
AC380V±10%,1.1kW
|
Dimensions (L×W×H)
|
940x745x1100mm
|
net weight
|
650kg
|
|
Technical advantages of rebar bending testing machine
As the construction industry's requirements for structural safety and quality control continue to increase, the quality management of rebar, as an indispensable core material in building structures, is particularly important. As a key device for detecting the bending performance of rebar, the rebar bending testing machine has shown significant advantages in improving test efficiency, accuracy and reducing human errors with its high-precision, fully automated testing functions. At the same time, the stability and safety of the rebar bending testing machine under high-load testing, as well as the enhanced traceability of the testing process, have made its application in quality control widely recognized and promoted.
High-precision, fully automated testing functions to reduce human errors
The high-precision testing function of the rebar bending testing machine is its most prominent technical advantage. Traditional manual testing methods often rely on the experience and judgment of operators, which is not only easily interfered by human factors, but also difficult to guarantee the accuracy and consistency of data. Especially when testing rebars in batches, manual operation may cause measurement errors, affecting the reliability of test results.
Unlike traditional manual testing methods, modern steel bending testing machines are equipped with advanced sensors, precision transmission systems and computer control technology, which can test the bending performance of steel bars with extremely high accuracy. The testing machine can accurately control the bending force, bending angle and loading rate applied to the steel bar, and automatically record the data during the test process to ensure that each test can obtain accurate and reliable results.
The automation function of the steel bending testing machine can reduce human errors, especially in the case of multiple tests and high-frequency operations. The automated equipment can maintain consistency and repeatability, avoiding the deviations that may occur in manual operation. This combination of high precision and automation not only improves the test efficiency, but also greatly enhances the credibility of the test results, making the control of steel quality more accurate and scientific.
Stability and safety under high-load testing
Another major advantage of the steel bending testing machine is its stability and safety under high-load testing. In construction projects, steel bars often need to withstand huge external forces. Therefore, in steel bending tests, the testing machine needs to be able to apply and withstand higher test loads. Some traditional testing equipment is prone to structural deformation or failure when working under high loads, resulting in inaccurate test results or even damage to the equipment.
Modern steel bar bending testing machines are designed with full consideration of the needs of high-load work, and adopt a high-rigidity frame and a powerful hydraulic system to ensure that the equipment can maintain stability and precision even when conducting high-load tests. The high-rigidity frame can effectively prevent the equipment from structural deformation when a large load is applied, ensuring that the stress state of the steel bar is accurately reflected during the test. The powerful hydraulic system can accurately adjust the test load and apply a large pressure in a short time to ensure that the bending performance of the steel bar under the limit load is fully examined.
The design of the steel bar bending testing machine focuses on the safety of the equipment, especially in high-load tests, where safety issues are particularly critical. Modern steel bar bending testing machines are usually equipped with a variety of safety protection devices, such as overload protection, emergency stop function, and automatic power off. These safety features can effectively prevent damage to the equipment when it is overloaded, protect the safety of the operator, and ensure that no accidents occur during the test.
Strengthen the traceability of the test process to facilitate quality review
With the increasing requirements for quality management and monitoring in the construction industry, especially in some important engineering projects, the quality inspection of basic materials such as steel bars must have a high degree of traceability. The steel bar bending testing machine can automatically record and store a large amount of test data throughout the test process through a modern computer control and data storage system. This efficient data acquisition and storage system not only ensures the accuracy of the test data, but also provides a complete record of the test process for quality review and traceability.
Specifically, the steel bar bending testing machine can record the test data of each steel bar, including bending force, bending angle, test time, tester and other information, which will be automatically saved in the equipment's database to form an electronic file. The test report can be automatically generated by the computer system and can be printed or exported as an electronic file for easy archiving and management. In this way, each test result has a complete historical record, and the specific test process and test data can be traced back at any time.
The traceability of test data not only helps to strengthen quality control, but also provides an effective basis for quality review. In construction projects, especially in large and high-risk projects, the inspection of steel bar quality often requires multiple levels of quality review and supervision. The rebar bending testing machine ensures that each test can truly and accurately reflect the performance of the rebar through its data traceability, making the quality management of the entire construction project more transparent and reducing the risks caused by data distortion or tampering.
The traceability of test data can also improve the speed of product quality improvement. If the bending performance of the rebar is found to be substandard in a certain project, the quality management personnel can quickly check all relevant data, quickly find the problem, and take targeted measures to improve it. For rebar manufacturers or suppliers, the traceability of test data is also an effective quality control method, which can help them to promptly discover and solve potential problems in production and further improve the quality of rebar.
Improve the accuracy of steel bar bending performance detection
As one of the core materials of building structures, the quality of steel bars is directly related to the safety and durability of buildings. In particular, the bending performance of steel bars is one of the key indicators of steel bar quality. In order to ensure the excellent performance and long-term reliability of steel bars in construction, the detection accuracy of steel bar bending performance is crucial. Through precision testing with a high-precision steel bar bending testing machine, it can be ensured that the bending performance of steel bars meets the design standards, unqualified products are discovered in time, and unqualified steel bars are prevented from entering the construction site, thereby improving the safety and quality assurance level of the entire construction project.
Ensure that the bending performance of steel bars meets the design standards through precision testing
The bending performance of steel bars not only determines its operability in construction, but also affects its bearing capacity, seismic resistance and durability during the use of buildings. In order to ensure that steel bars can play their expected functions in actual use, the bending performance of steel bars must be strictly tested. The detection of steel bar bending performance includes testing of multiple indicators such as its bending angle, bending strength, and ductility. Only through precision testing can it be ensured that the steel bars meet the design standards.
Accurate detection of bending angle: In the steel bar bending test, the bending angle is a very important parameter. Usually according to the design requirements, the steel bar needs to complete the bending operation at a specific angle. Modern steel bar bending testing machines are equipped with high-precision sensors and angle measurement systems, which can accurately measure the bending angle of the steel bar and compare it with the design standards. Only when the steel bar is within the specified bending angle range can it be proved that it has good bending performance and can be used smoothly during the construction process.
Precision testing of bending strength and yield strength: Bending strength and yield strength are two key indicators in the bending performance of steel bars, which directly affect the deformation capacity and bearing capacity of steel bars when subjected to external forces. The steel bar bending testing machine can accurately measure the bending strength and yield strength of steel bars by accurately controlling the applied force and testing the bending response, and compare them with the design requirements. If the bending strength and yield strength of the steel bar do not meet the standard, it means that it may suffer brittle fracture or deformation during use, affecting the structural safety of the building.
Inspection of ductility and plastic deformation capacity: The ductility and plastic deformation capacity of steel bars are important indicators to measure their bending performance. Through the high-precision control system of the steel bar bending testing machine, it is possible to accurately test whether the steel bar can undergo a certain plastic deformation without breaking during the bending process. The modern steel bar bending testing machine adopts advanced mechanical simulation technology, which can comprehensively analyze the stress changes of the steel bar during the bending process to ensure that it has sufficient ductility and plastic deformation capacity to meet the design requirements.
Multiple bending tests and reverse bending: The steel bar may encounter multiple bending or reverse bending during the construction process, especially in seismic design and structural connections, where the steel bar will experience repeated stress. Through the steel bar bending testing machine, the performance changes of the steel bar under multiple bending and reverse bending conditions can be simulated to comprehensively evaluate the fatigue strength and crack resistance of the steel bar. Through precision testing, it can be ensured that the steel bar will not experience performance degradation or breakage under these special use conditions, thereby meeting the high standards of construction projects.
Timely detection of unqualified products and prevention of unqualified steel bars from entering the construction site
The steel bar bending testing machine not only plays an important role in detecting the bending performance of steel bars, but also helps quality control personnel to timely detect unqualified products and prevent unqualified steel bars from entering the construction site through efficient and accurate detection functions, thereby ensuring the overall quality of the construction project.
Real-time detection and judgment: The steel bar bending testing machine can collect test data in real time and compare and analyze it with the design standards. If the bending performance of the steel bar fails to meet the specified requirements, the test machine will automatically alarm and terminate the test. This instant feedback function effectively avoids manual misjudgment or delays, ensuring that unqualified steel bars are screened out in time.
Batch detection and automatic screening: In large-scale construction projects, the purchase and use of steel bars are huge, and how to conduct quality inspections on a large number of steel bars in a short period of time has become an important issue. Modern steel bar bending testing machines are equipped with an automated batch detection system that can automatically test a large number of steel bars. The testing machine can automatically identify and record the bending performance of each steel bar and generate a detailed test report. If the bending performance of a certain steel bar is unqualified, the system will automatically mark it as an unqualified product to prevent it from entering the construction site and ensure the quality of materials during the construction process.
Improve detection efficiency: Traditional steel bar quality inspection methods usually rely on manual inspection, which is not only inefficient, but also easily affected by human factors. The steel bar bending testing machine can significantly improve the testing efficiency through automated operation, especially when inspecting large quantities of steel bars, which can reduce the inspection cycle and increase the speed of quality management. In engineering projects, quickly screening out unqualified steel bars can save a lot of manual inspection time and provide guarantee for construction progress.
Prevent unqualified steel bars from affecting the overall construction quality: In construction projects, steel bars are a key component of load-bearing structures. Any unqualified steel bar may affect the safety and stability of the entire structure. Through the precise detection of the steel bar bending testing machine, these unqualified steel bars can be effectively prevented from entering the construction site, ensuring the quality of the construction from the source. If unqualified steel bars are mixed into the construction site, it may lead to a decrease in structural bearing capacity, poor durability, and even safety accidents. The precise detection of the steel bar bending testing machine ensures that each steel bar can play its expected role in construction, thereby ensuring the long-term safety of the building.
Automated operation and efficiency of steel bar bending testing machine
With the continuous improvement of quality requirements in the construction industry, traditional steel bar quality inspection methods have been unable to meet the efficiency, accuracy and safety requirements of modern construction projects. As a key inspection equipment, the steel bar bending testing machine has significantly improved the testing efficiency, reduced the errors of manual operation, and optimized the workflow of the inspection process with its automated operating system. Through automated operation, the steel bar bending testing machine not only reduces the labor intensity of operators, but also greatly improves the accuracy and consistency of test data, providing reliable guarantee for steel bar quality control.
How does the automated system reduce manual operation and reduce labor intensity
Automated operation is a highlight of modern steel bar bending testing machines, especially in large-scale steel bar testing and repetitive testing, where the automated system plays an important role. Traditional steel bar bending tests often rely on manual operation, which is not only cumbersome to operate, but also often has a large time consumption and labor intensity in batch testing. In a manual operation environment, personnel fatigue, distraction and operational errors may affect the accuracy of the test results. The introduction of automation effectively reduces these human interferences and improves work efficiency.
Fully automated loading and unloading system: Modern steel bar bending testing machines are equipped with fully automated loading and unloading systems that can automatically place steel bars on the test bench and test them according to the set procedures. Traditionally, operators need to manually load steel bars into the equipment and adjust parameters according to different test requirements. Manual operation is time-consuming and error-prone. The automated system can complete these tasks through the preset mode of the program without manual intervention, and the operation is more convenient and efficient. The automated loading system not only saves the time of manual handling, but also reduces the damage or error of steel bars that may be caused during the handling process.
Intelligent control system and automated parameter setting: The automated control system enables all aspects of the testing process to be intelligently controlled through programming. The operator only needs to enter the relevant test parameters, and the system will automatically adjust the load, bending angle, test speed, etc. of the testing machine and automatically perform the test. During the entire test process, the operator does not need to repeatedly adjust and monitor the equipment manually. All operations can be completed automatically by completing the configuration at the initial setting. This intelligent control greatly reduces the number of manual interventions and reduces the risk of operational errors.
Automatically record and analyze test data: The automated system can not only complete the automatic operation of the test, but also automatically record various data during the test, including bending force, angle, yield strength, test time, etc. The test results are recorded in real time and saved to the computer system, and the operator can easily view, export or print the test report. Compared with the traditional manual data recording method, the automated data acquisition and processing system eliminates errors in manual entry, speeds up data processing, and ensures the accuracy of the test results.
Reduce operator errors and improve data accuracy and consistency during batch testing
Batch testing is a common situation in steel bar quality control in the construction industry, especially in large-scale engineering projects, where a large number of steel bars need to be quickly and accurately inspected. Traditional manual testing methods make it difficult to ensure that operators can maintain a high degree of concentration and avoid errors in high-intensity and high-frequency working environments. The automated operating system of the steel bar bending testing machine significantly improves the efficiency and accuracy of the test through intelligent control, ensuring that the test data of each steel bar in batch testing is accurate.
High-precision data acquisition and error-free recording: The automated system can accurately record the test data of each steel bar, including key indicators such as bending load, deformation angle, and yield point. After each test, the data is automatically saved and a standardized test report is generated. The high-precision sensors and control systems of the automated system ensure the accuracy of data acquisition and avoid the interference of human errors. For example, the collection of test data is not affected by factors such as the operator's physical strength and emotions, so the consistency and accuracy of the data are fully guaranteed during continuous operation.
Reduce human operation errors and subjective deviations: Since the operation of the steel bar bending testing machine has been automated, human errors in the test process are significantly reduced. Traditional manual operation may cause measurement errors or result deviations due to operator negligence, fatigue or lack of experience. The automated system uses a set of preset test procedures to not only reduce the interference of human factors during the test, but also eliminate the subjective deviation of the operator. For example, the test parameters such as the bending angle and bending load of the steel bar will be accurately controlled, and the system will automatically determine whether the steel bar meets the standard, and unqualified products will not flow into the market due to human subjective judgment errors.
Improve test efficiency and shorten test cycle: The introduction of automated operation has greatly improved test efficiency, especially in batch testing. Traditional manual testing methods, especially repeated testing links, are prone to long test time and low efficiency, while automated systems can complete multiple tests in a very short time. For example, the rebar bending testing machine can automatically perform bending tests of multiple rebars by setting different test programs. Each test item can be successfully completed under the automatic control of the equipment, thereby greatly shortening the time of the entire batch test. Automated testing can also process multiple samples at the same time, increasing the number and coverage of tests, thereby improving the work efficiency of the entire quality control.
Big data analysis and trend prediction: Another major advantage of the automated rebar bending testing machine is that it can summarize and analyze a large amount of test data and make trend predictions based on the data. Through intelligent analysis of historical data, the system can identify the trend of changes in rebar quality, help quality management personnel to promptly discover potential problems, and take effective measures to improve them. This big data analysis function not only improves the efficiency of testing, but also provides a scientific basis for quality management, helping managers make more accurate decisions.
Importance of steel bar bending testing machine to building quality control
In construction projects, steel bars are key materials for building structural stability and bearing capacity. The bending performance of steel bars directly affects the safety and durability of buildings, especially in special cases such as external forces or vibrations. Whether the steel bars can maintain sufficient plasticity and strength determines whether the building can withstand various loads during use. As an important tool for steel bar quality inspection, the steel bar bending testing machine effectively prevents the occurrence of quality risks while ensuring that the bending performance of steel bars meets the standards, and has become an indispensable part of building quality control.
Through actual case analysis, the steel bar bending testing machine not only plays a vital role in standardized testing, but also effectively improves the overall quality of construction projects and avoids serious quality problems caused by unqualified steel bars.
Standardized testing process to prevent quality risks
The steel bar bending testing machine can ensure that the bending performance of steel bars meets the design requirements through a series of standardized testing processes, and prevent hidden dangers caused by steel bar quality problems in construction projects from the source. Here are some key standardized testing processes that play a vital role in construction projects:
Inspection and quality traceability of steel bars
Each batch of steel bars needs to undergo strict inspection before entering the construction site. At this time, the steel bar bending testing machine plays a key role. The steel bars must first undergo a cold bending test to test their bending strength, yield point and ductility to ensure that they meet the design requirements. This link of inspection can not only ensure that the performance of the steel bars meets the standards, but also trace the production source and quality records of each batch of steel bars to prevent inferior steel bars from entering the market.
The precision test of the steel bar bending testing machine can detail the performance parameters of each steel bar through real-time data recording and test reports. If a batch of steel bars has problems during the test, the system will automatically alarm, and the relevant personnel can replace or scrap the unqualified materials at the first time to ensure that every steel bar used in the construction project meets the quality standards.
Regular sampling during construction
The quality inspection of steel bars is not only an inspection at the time of entry, but also requires regular sampling during the construction process. Especially in large-scale construction, random sampling of used steel bars is carried out to ensure that the steel bars are not damaged or deformed during the construction process. The steel bar bending testing machine can quickly complete the sampling at the construction site and provide accurate test results to ensure that the steel bars always meet the predetermined standards.
Traceability and analysis of test data
The steel bar bending testing machine can not only generate accurate test data, but also record and archive every detail of the test process. The test results include bending force, bending angle, yield strength and other information, which can be accurate to each steel bar. The traceability of test data allows quality management personnel to easily check the historical test data of each batch of steel bars, trace the source of the product, and ensure the reliability of the test results.
In engineering quality control, data accuracy and traceability are crucial. For example, if a building has a structural problem, the quality management personnel can quickly find the problem by tracing back the test data and take timely measures to repair it. Through this standardized testing process, hidden dangers caused by steel bar quality problems can be effectively avoided.
Final inspection and quality acceptance
Before the completion of the construction project, the quality control of the steel bars cannot be relaxed. The final quality acceptance link must ensure that all the steel bars used meet the standard requirements. The steel bar bending testing machine can conduct a detailed inspection at this stage to ensure that the bending performance of all the steel bars used in the construction has passed the test. If any unqualified steel bars appear, the acceptance personnel can request a replacement in time to ensure the overall quality of the building.